More About UAV Design and Developing
- aerialdynamictech
- Oct 26, 2021
- 3 min read
As a professional UAV design and developing company, we can complete a 100% full-process aircraft design solution from conceptual requirements to production process.
Step 1: Know Customer Needs:
Clarify the customer's usage scenarios, specifications requirements and special functional requirements, and initially clarify the UAV size and configuration.
Step 2: Layout Configuration Selection:
According to the design requirements, select the VTOL type, as well as basic aerodynamic configuration of the aircraft, such as VTOL conventional configuration fixed wing, UAV single-rotor helicopter, or Hexa-rotors UAV.
Step 3: Propulsion Systems Design and Integration:
Development and integration according to customer's functional and performance requirements, then determine the type of propulsion system, and select and design specific models, such as motor model, gasoline piston engine model, turbojet engine model, turboshaft power system design, hybrid power system design and so on.
Step 4: Concept Plan Evaluation:
According to customer's functional and performance requirements, our R&D team can quickly provide a preliminary overall conceptual design, sketch the solution as a freehand sketching, generate a two-dimensional schematic drawing, then simple 3D UAV drawing, in this way, to efficiently, intuitively, and accurately present the UAV design proposal to customers

Step 5: Aerodynamic Design:
The Aerodynamic design is a very significant step in a whole UAV R&D project, Our R&D team are using theoretical analysis methods, vortexlattice method, CFD method, etc., iteratively calculate the airfoil data, aerodynamic shape parameters, aerodynamic performance indicators and so on that meet the functional and performance requirements, and create the digital modeling of the whole machine shape in Catia.

Step 6: Aerodynamic Optimization Analysis:
In this step, our R&D team will run CFD multi-modal aerodynamic simulation for the whole UAV or partial shape (Wings, fuselage, VTOL motors Wing Mount..etc), and proceed detailed shape modifications basically according to the simulation results, then maximize aerodynamic performance, obtain accurate and complete aerodynamic parameters without changing the overall aerodynamic scheme.
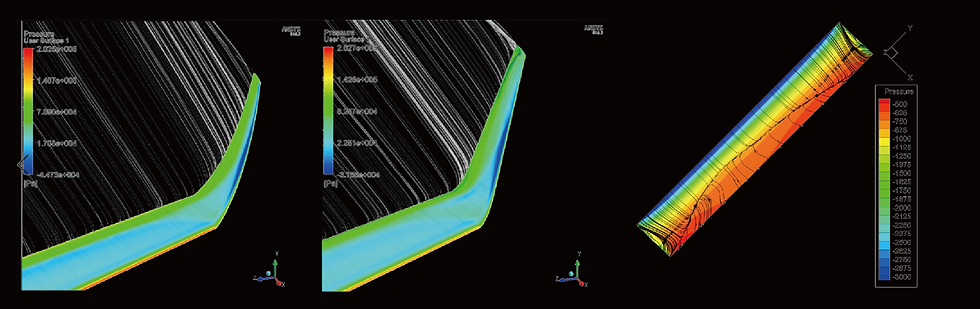
Step 7: Equipment and System Layout:
In order to correctly determine the location and layout of airborne equipment such as payload, battery, flight controller, communication equipment, servos, another sensors, companion computer etc., our R&D team must carefully complete a comprehensive assessment of the CG (center of gravity) of the aircraft, flight operation stability requirements, and equipment location requirements.

Step 8: Structural Mechanical Design:
The design details 3D modeling such as the internal structure of the aircraft, surface treatment, flaps, canopies for the payload and battery bays, connection mechanisms of each separation surface( wing and fuselage joint surface), installation and mounting of payload or equipment, mechanical structure of transmission system, etc. must be completed before entering the next step.
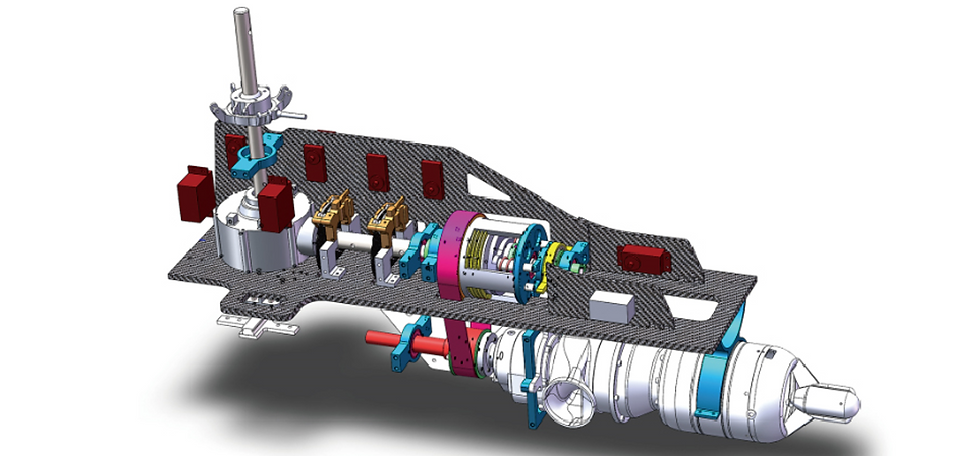
Step 9: Structural Optimization Analysis:
Our R&D team will use the FEM finite element analysis method to perform accurate load analysis on key structural components (such as spars, joints, spindles, etc.), and make adjustments to the structure to ensure that It achieves an efficient strength-to-weight ratio as well as keep it fly safely.
Step 10: Flight Performance Evaluation (Software):
We will determined in the overall design, the flight performance of the aircraft (such as maximum flight time, maximum range, maximum climb rate, maneuverability, stability, etc.) and perform calculations according to the aerodynamic parameters, weight parameters, power system parameters, etc.

Manufacturing and Processing:
We will design the most cost-effective aircraft processing technology and mechanical construction processing plan according to customer needs, manufacturing plans including composite materials (glass fiber, carbon fiber, PMI, honeycomb materials, kevlar materials), surface quality (painting in the mold, roughness requirements, etc.), mold type (substitute wood mold, glass fiber reinforced resin mold, metal mold, etc.), molding method (hand spreading process, pre-dipping processing).
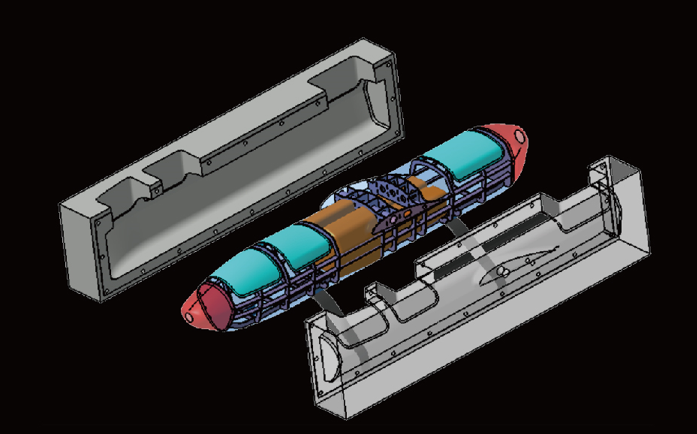
We also do custom made UAV components R&Ds:
Propeller Design and Flow-field Analysis:
Our R&D team can analyze and determine the operating conditions of the propeller, and use the CFD turbulence model to design or optimize the appropriate propeller airfoil, blade configuration, disk size, number of blades, propeller diameter, distribution, thickness distribution and other key design parameters , And optimize the blade tip modification according to the stall characteristics, and design the blade root according to the structural characteristics.

Helicopter Rotor Design:
According to the flight conditions of the helicopter, analyze and determine the best rotor working speed and paddle load, obtain the basic circulation distribution through the Blade element momentum theory, and determine the required rotor solidity according to the paddle load, which is the key in the span direction Design or optimize a suitable airfoil and its torsion angle at the section, and finally focus on the optimization of the blade tip according to the forward flight speed or noise control requirements of the helicopter.

Detail CAD Design
According to customer needs, complete 1:1 digital modeling of detailed structures including wires, screws, hinges, painting, etc., and create corresponding perspective drawings, renderings, and cross-sectional views.

Industrial Design
Our R&D can fulfill customers' industrial design needs such as innovative appearance, structural innovation, CMF, functional layout optimization, human-computer interaction interface, and ergonomic design.
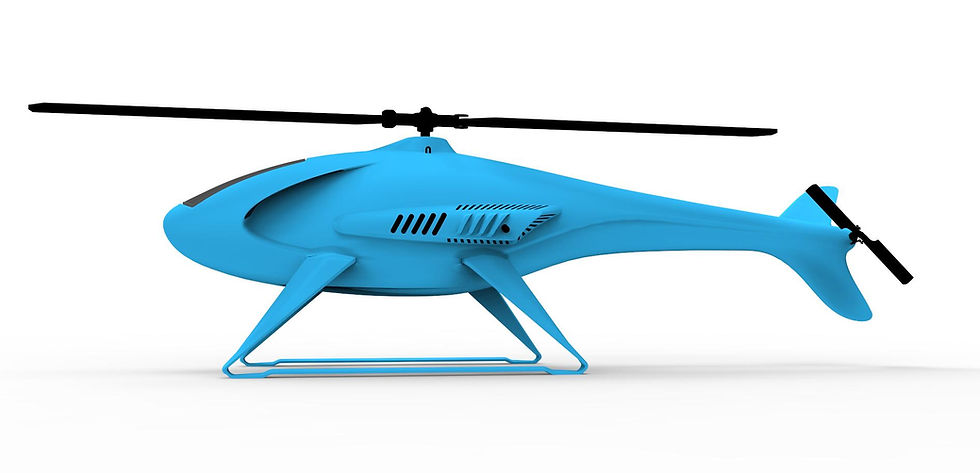
In-depth Analysis of Aircraft Specialization:
1. Flight Dynamics Analysis

2. Analysis of the Strength and Stiffness of Key Components
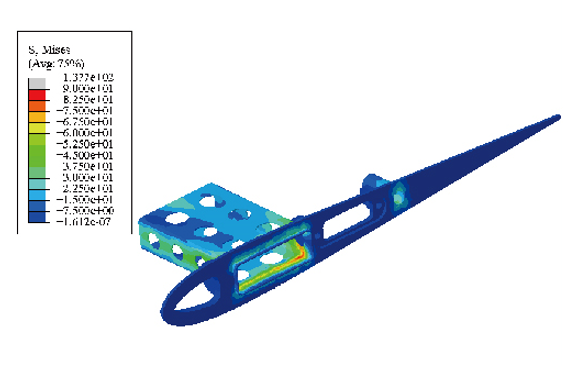
3. Aerodynamic Elasticity Analysis

4. Flight Envelope Calculation

5. Composite materials Finite Element Analysis

Comments